
在钢铁行业转型升级的浪潮中,如何用最小投入实现最大效能始终是工业现场管理的核心命题。集团炼铁厂公辅二工场供料股的创新实践给出了答案——仅用千元级成本便破解了困扰车间十年的混料顽疾,更开辟出一条绿色低碳的工业现场改造新路径。这个充满智慧的小微改造案例,生动诠释了"创新不在大小,关键在精准"的管理哲学。
背景与痛点:环境与人员双重挑战
炼铁厂公辅二工场供料股长期面临两大难题:一是现场环境复杂,除尘管道陈旧锈蚀,二是料仓管道标识字体由于年久模糊不清,视觉辨识度低,会频繁导致混料、错料问题。据统计,2024年因混料引发的炉况波动达11次,每次炉况波动都会带来不小的经济损失。如何破解“工作环境”与“人员操作”不协调的问题,成为炼铁厂供料股车间亟待解决的难题。

破局思路:从“视觉改造”到“防错体系”
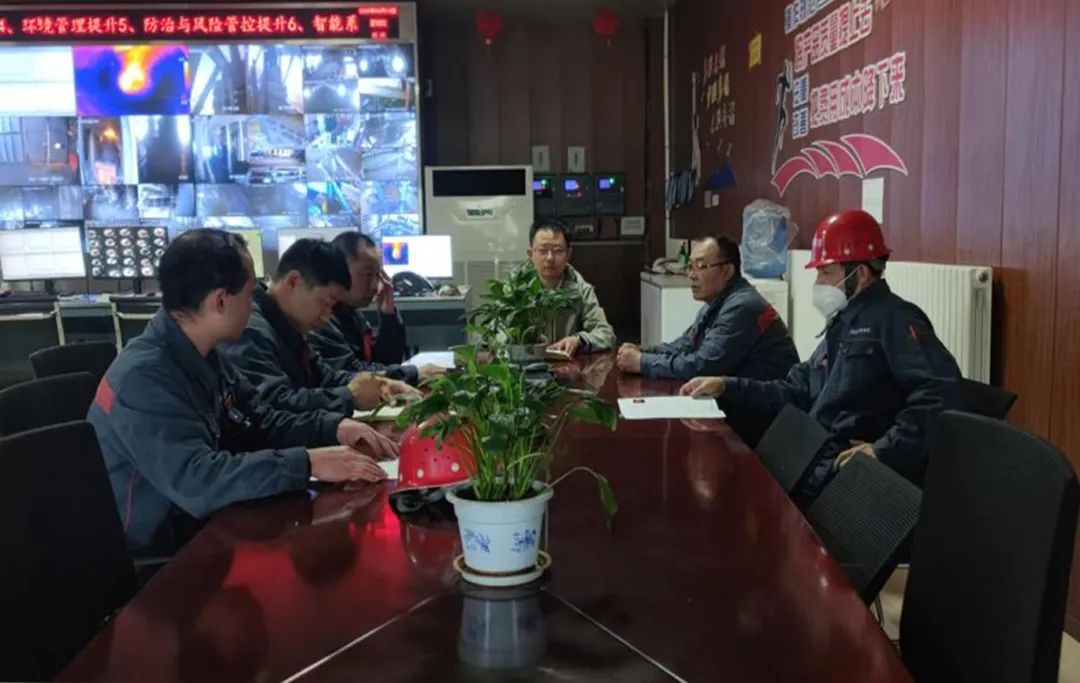
在集团战略引导下,2024年10月初,炼铁厂成立专项小组,由生产副厂长于超群牵头,组建防混料技术攻关,由公辅副主任杨凯负责执行实施。通过3个月的现场不断调研观察、员工访谈及事故溯源,发现混料事故多集中于物料输送路径辨识不清环节。经反复论证,团队提出“以颜色代文字、以色标定规则”的创新路径,即利用高对比度色彩区分物料种类,以此提升辨识度,同步对除尘管道进行刷漆美化,将功能优化与环境整治深度融合。
方案落地:科学设计与精准实施
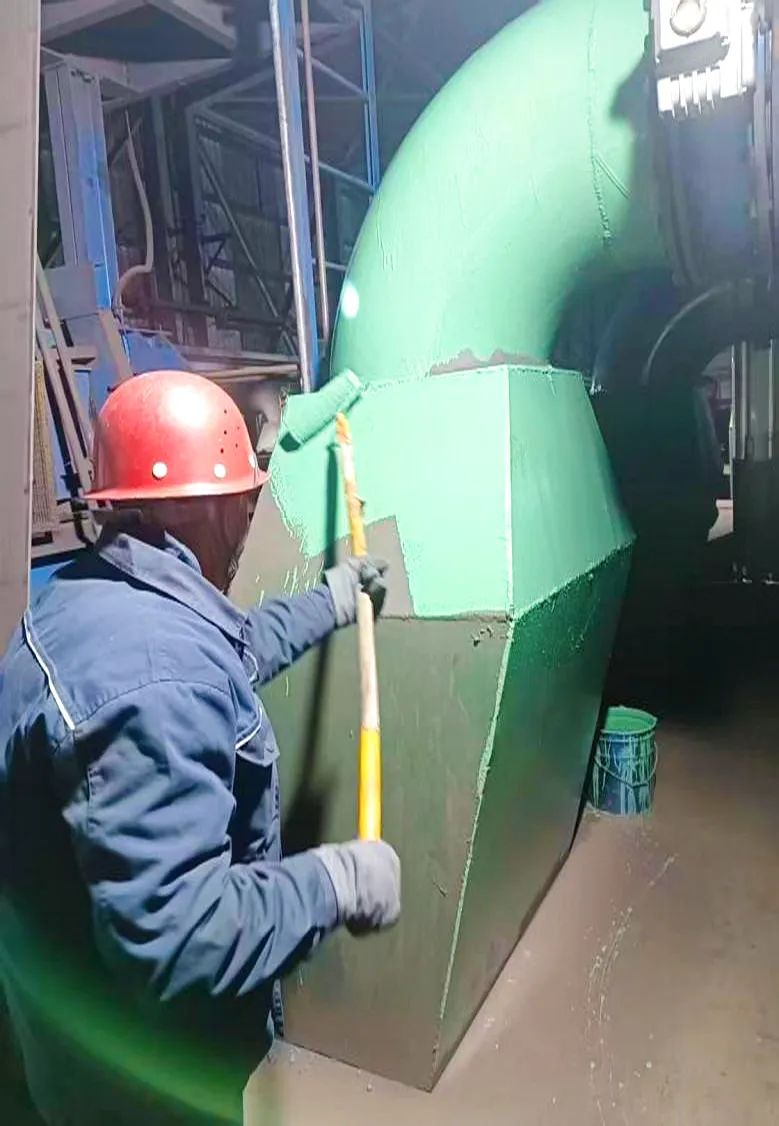


色彩编码体系构建:依据物料特性与生产逻辑,选定6种高辨识度颜色,车间对128个料仓顶部除尘管道采用多种颜色油漆整体翻新,并在料仓对应管段设置环形色带,以红、黑、绿、黄、蓝、灰六色分别标识球团、块矿、焦炭、烧结、辅料(硅石+蛇纹石),并配有手喷式字体标识牌,30米之内清晰可见,确保远距离精准辨识。
现场美化与功能整合:改造后,管道锈蚀率降低95%,设备清洁周期从7天延长至10天,现场整洁度显著提升,员工目视化操作效率提高,现场美观度与功能性同步优化提升。
成效与启示:小成本撬动大变革
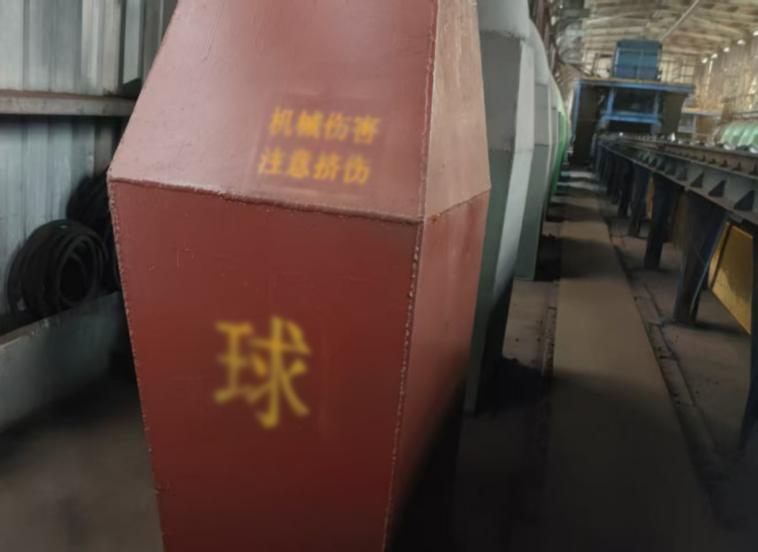
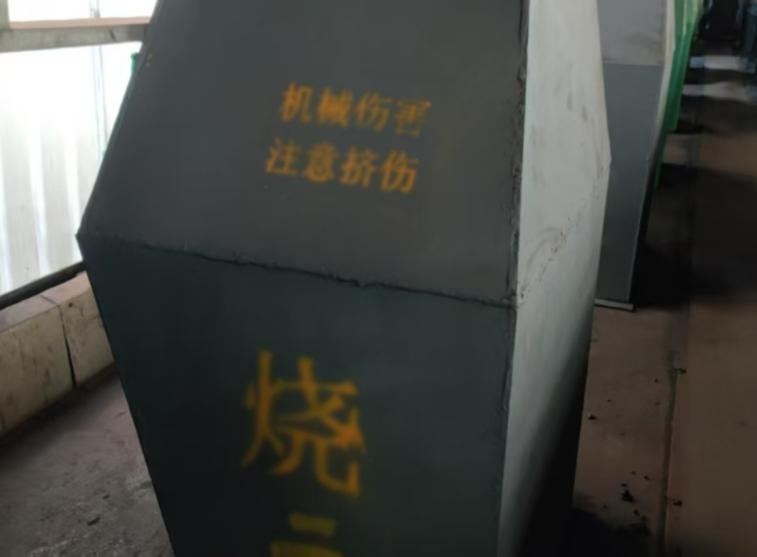
混料风险大幅下降:2025年第一季度,员工物料识别准确率超99%;混料事故率由月均1-2次降至0次,降幅达99.8%;新员工培训周期缩短40%,减少培训时间,能够快速适应现场生产节奏;高炉炉况得到稳定性提升。
管理范式创新价值:车间建立色标维护规范,定期巡检保障色彩标准统一,为安全生产筑牢防线。该方案以低成本实现高效能管理,通过“颜色赋能”替代复杂技术改造,形成可复制的“防错模型”,已推广至全厂开展。
五、结语

炼铁厂的实践证明,传统制造业的痛点往往蕴藏创新突破点。炼铁厂厂长王长纯对于此次技改给予高度赞扬与肯定,并授予公辅二工场优秀团队锦旗,他讲到:“通过将人性化设计与科学管理工具结合,用‘看得见的颜色’破解‘看不见的风险’,不仅实现了降本增效,更探索出一条低成本、绿色化的工业现场改造路径。”集团这一案例为行业提供了宝贵启示:技术创新未必需要高精尖,立足实际需求的“小微改造”同样能释放巨大生产力。